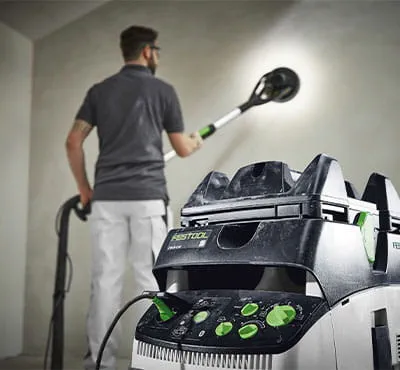
Healthy and safe work
Healthy working and occupational safety are often neglected, especially in small and medium-sized enterprises – although employees in the construction industry are known to be among the professional groups with the highest risk. For this reason, awareness of health and safety at work should be constantly increased, especially in such companies. It pays off in the long run because healthy employees are the most important capital in any company. What the statistics look like and what can be done is presented in three parts. News about mixing with dust extraction.
In everyday working life, legal requirements and regulations for healthy working and safety at work are often seen as an annoying duty. They pose organisational challenges, especially for small and medium-sized enterprises (SMEs). However, the long-term benefits, such as higher productivity and competitiveness, are convincing. Occupational health and safety measures contribute to the prevention of accidents, reduce absences and lower the cost of continued pay.
- 50.8% of the days absent from work in the trades sector are attributable to long-term illnesses (over 42 days) (Source: IKK classic report 2018 Germany)
- Employees in the trades sector are absent from work because of musculoskeletal disorders (33.5%), injury and poisoning (17.2%) and respiratory illnesses (14.5%) (see above source).
The "Safety and Health at Work" report published in 2019 by the Federal Institute for Occupational Safety and Health (BAuA) on behalf of the Federal Ministry of Labour and Social Affairs (BMAS) shows that prevention measures are effective. According to this report, there were 33% fewer fatal accidents at work and 15% fewer reportable accidents at work in the metal and electrical industry in 2018 than in previous years.
Risk assessments as a basis for healthy working and occupational safety
Risk assessments form the basis for suitable and effective measures to make working in the company safer and healthier. These are well worth the effort because weak points within the company can be identified and eliminated. Carrying out a risk assessment is thus part of the principle of a "continuous improvement process" (CIP) and results in higher productivity. The respective scope of a risk assessment is based on the operational requirements and conditions. All known work processes are recorded. This also includes events and tasks that take place outside "normal" operating conditions, such as maintenance work, commissioning and decommissioning, procedures in the event of breakdowns, cleaning work or waste disposal. Depending on the size of the company, the management or respective team leaders carry out the assessment. The employees are actively involved, as they themselves are best acquainted with the operational work processes, the risk factors and the protective measures implemented so far.
The exact procedure of the assessment is determined individually. The Institute of Applied Industrial Engineering and Ergonomics (ifaa) provides further assistance in this respect.
It's worth the effort
Every employee matters, especially in small companies. Any absence due to an accident or illness has a negative impact on the operating result.
Studies have shown that every euro invested in occupational safety and health is money well spent, because every euro invested is worth twice as much (International Social Security Association, ISSA)
Even simply purchasing safety shoes, work gloves, protective goggles and breathing masks increases safety and protects health. Festool, a German company, supports healthy work with a wide range of different mobile dust extractors. Philipp Stahl, Application Engineer at Festool, has this to say: "During renovation work and substrate preparation, in particular, sanding down cement-based filler, plaster filler, plaster or clear coats generates a huge amount of dust which is made up of particles that can cause permanent damage to your lungs and airways. Dust-free work is therefore imperative and with the suitable mobile dust extractors and the right system accessories from the dust extraction and sanding ranges, Festool provides the ideal all-inclusive package for painters, floor tilers, drywallers and all renovation and restoration companies.
NEW: Dust-free mixing at last - The new MX stirrers with dust extraction allow users to mix and stir in a healthy way Dust-free work begins with mixing. This is why Festool will offer its new MX stirrers with dust extraction since January 2021. They are sophisticated in every detail since they are equipped with a new hoop guard, convenient ErgoFix height adjustment, stable rubber corners, smooth start-up and a high-torque motor. This will allow painters, drywallers, plasterers and all other renovation professionals to mix and stir in a robust, ergonomic and, above all, healthy way.
After all, it does not take much to protect yourself and your employees. Efficient dust extraction is so easy and quick to set up that you can get to work immediately. The right combination of a sander, abrasive and mobile dust extractor is crucial for low-dust work. The mobile dust extractor is the deciding factor here – its extraction and filter performance must be exactly right, so that the dust which has formed can be directly extracted, not thrown into the air. In this respect, the CTM 26 E AC, CTM 36 E AC and CTM 36 E AC HD mobile dust extractors with dust class M and Autoclean function are ideal for all painting and decorating renovation work. The more compact CTM 26 E AC, with its container capacity of 26 litres, is particularly suited tosmaller areas and the larger CTM 36 E AC and CTM 36 E AC HD mobile dust extractors with a container capacity of 36 litres are particularly effective on larger surfaces."
Information about Festool is available at www.festool.co.uk
You will find the press releases in all languages in the media set.